Introduction
Foundries are critical to industries that involve metal casting, mold-making, and high-temperature processes. The application of high-temperature materials in foundries is essential to improving efficiency, ensuring durability, and optimizing energy consumption during metal melting, heating, and other high-heat tasks.
In this guide, we will explore the essential high-temperature materials used in foundries, including silicon carbide heating elements, crucibles, and ceramic fiber products. We’ll also discuss how these materials play a pivotal role in optimizing foundry operations and enhancing overall production performance.
1. What is a Foundry and Why High-Temperature Materials are Critical?
A foundry is a factory where metals are melted and poured into molds to form a variety of shapes. The process involves extremely high temperatures, often exceeding 1000°C, requiring specialized materials capable of withstanding such conditions.
High-temperature materials, such as heating elements and crucibles, are vital in foundry operations for tasks like metal melting, heat retention, and thermal insulation. For a deeper understanding of how these materials withstand extreme conditions, check out our article on Understanding Refractories: Essential Materials for High-Temperature Applications, which explores the role of refractories in high-temperature applications. To learn more about how these materials enhance thermal efficiency, check out our comprehensive guide on ceramic fiber insulation, which delves into key insulation solutions. These materials help improve the efficiency of the foundry process and ensure that the metal does not cool prematurely or become contaminated.
For more details on industrial heating elements, visit our Industrial Heating Elements Guide, where we showcase products like silicon carbide heating elements that are perfect for high-temperature environments.
2. Essential High-Temperature Materials Used in Foundries
Foundries rely on a range of high-temperature materials to perform various tasks in metalworking. Some of the most commonly used materials include:
- Silicon Carbide Heating Elements: These are used in furnaces to provide efficient, high-temperature heating for metal melting and other processes.
- Crucibles: These are containers used to hold molten metal. Silicon carbide crucibles, for example, are highly resistant to heat and thermal shock.
- Ceramic Fiber Products: Products such as ceramic fiber blankets, modules, and boards are used for insulation purposes, minimizing heat loss and improving energy efficiency.
Each of these materials has unique properties that make them essential in foundry applications. For instance, silicon carbide heating elements are known for their high thermal conductivity and durability in high-temperature environments.
Learn more about the properties of these materials in our comprehensive guide on Fire Bricks, which are also used for insulation in high-temperature processes.
3. How Silicon Carbide Heating Elements Revolutionize Foundry Operations
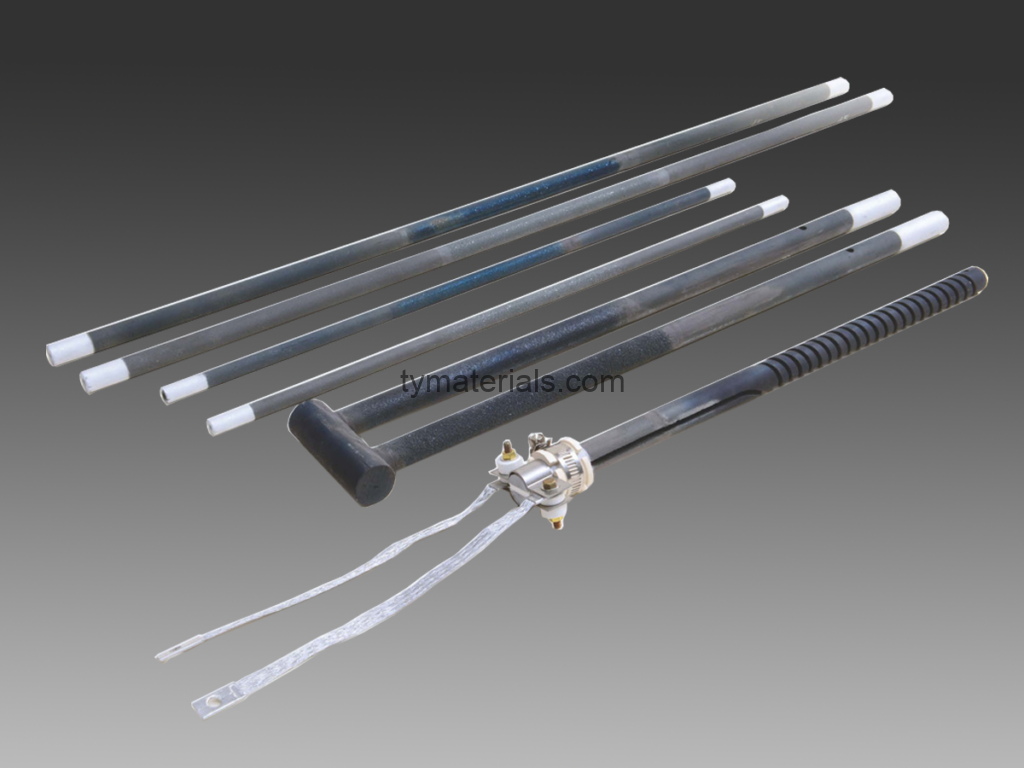
Silicon carbide heating elements play a transformative role in foundry operations. Due to their ability to withstand extreme temperatures and their excellent thermal conductivity, they are commonly used in furnaces and kilns. For more information on how silicon carbide heating elements perform in metal melting, explore our guide on Aluminum Melting Pot: Essential for Efficient Metal Casting to understand how they work together with other foundry materials.
For example, the double spiral silicon carbide heating element is designed to offer higher heat output with minimal energy consumption, helping foundries achieve better melting efficiency.
Explore our Silicon Carbide Heating Elements page to learn more about how these elements can enhance your foundry operations.
4. The Role of Crucibles in Metal Melting and Foundry Operations
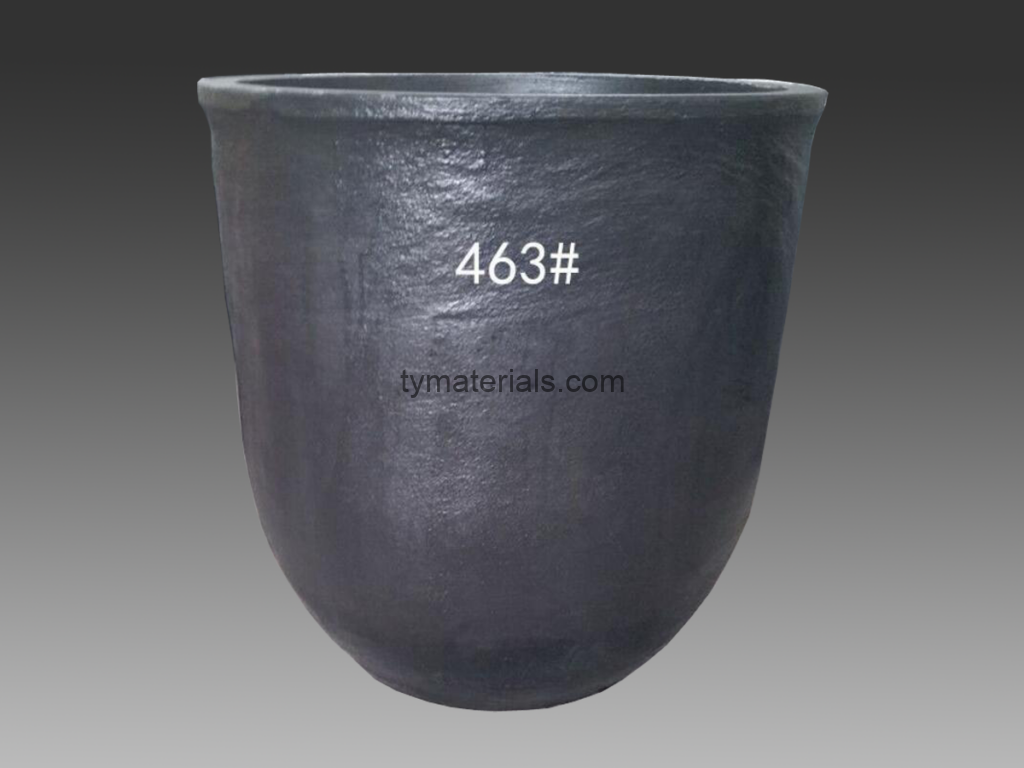
Crucibles are essential tools in any foundry, used to hold molten metals during the melting process. The choice of crucible material significantly impacts the quality of the final product. Silicon carbide crucibles, for example, are highly resistant to heat and thermal shock. For further details on how silicon carbide crucibles perform in high-temperature applications, check out our Silicon Carbide Crucible Guide.
Selecting the right crucible is crucial to ensuring that the melting process runs smoothly and that there is no contamination of the molten metal. Learn more about the importance of selecting the right silicon carbide crucibles by visiting our Silicon Carbide Crucible page.
5. How Ceramic Fiber Insulation Enhances Foundry Efficiency
Ceramic fiber products, such as blankets, modules, and boards, are essential for insulating high-temperature equipment in foundries. They help reduce energy consumption by minimizing heat loss, while also improving safety by containing high temperatures. To learn more about how ceramic fiber insulation optimizes energy efficiency, visit our Ceramic Fiber Insulation page.
In foundries, these materials are commonly used to insulate furnaces, kilns, and melting pots, providing both thermal protection and energy savings. Ceramic fiber modules and ceramic fiber boards are especially effective in protecting against heat loss during metal melting processes.
To find out more about ceramic fiber insulation options, visit our Ceramic Fiber Products page for detailed product specifications and applications in high-temperature industries.
6. Conclusion
High-temperature materials are the backbone of every foundry operation. From heating elements that provide reliable and efficient heating to crucibles that ensure molten metal is safely contained, these materials significantly impact the performance of foundries worldwide. By choosing the right materials, you can optimize your foundry’s efficiency, reduce energy costs, and improve product quality.
For more information on how these high-temperature materials can revolutionize your foundry operations, check out our detailed guides on Fire Bricks, Ceramic Fiber Insulation, and Aluminum Melting Pots, which provide a deeper understanding of essential foundry materials.
External Links:
- To gain a deeper understanding of the foundry industry and stay updated on the latest trends and technologies, visit the Refractories Worldforum, a leading industry resource for refractory materials and foundry applications.
- For industry standards and certifications related to foundries, check out ASTM and ISO.